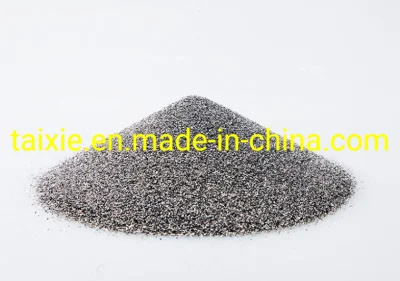
Microcarbon Ferrochrome 65V6 65V3 70V3 Welding Industry Powder Metallurgy
Description
Basic Info.
Model NO. | Pure molybdenum gasket Polish the molybdenum gaske |
Composition | Cr 60-75%, C 0.03-0.10% |
Transport Package | Packed in Wooden Cases/Iron Drums |
Specification | High temperature molybdenum wire diameter 0.18mm 0 |
Trademark | taixie |
Origin | China |
HS Code | 7806009000 |
Production Capacity | 500 / Ton |
Product Description
Name:Microcarbon ferrochrome | Spec: | ||
Chemical composition: | SIZE: | ||
National standard | Test results | ||
Cr | 60.0-70.0 | 65.49% | |
C | 0.06% | 0.054% | |
Si | 1% | 0.66% | |
S | 0.025% | 0.015% | |
P | 0.3% | 0.025% | |
FE | 40-60 | ||
Liquidity (S/50g) | |||
Apparent Density(g/cm²) | |||
plastic(g) |
Microcarbon ferrochrome 65V6 65V3 70V3 welding industry powder metallurgy
A micro-carbon ferrochrome powder is provided. The weight percentage of each component in the micro-carbon ferrochrome powder is as follows: 60-80%; Toner 0.03-0.045%; Silica powder 0.85-1.28%; Phosphorus powder 0.015-0.032%; Sulfur powder 0.015-0.028%; The beneficial effects of the invention are as follows: the micro-carbon ferrochrome powder of the invention has reliable and reasonable composition ratio, high utilization rate in the smelting process, and produces less pollution and impurities, has good economic value and use value, and meets the requirements of green sustainable development.
The method of making high nitrogen steel with micro-carbon ferrochrome is to first make high nitrogen ferrochrome intermediate with micro-carbon ferrochrome powder, and then make high nitrogen steel with high nitrogen ferrochrome intermediate. This method uses micro-carbon ferrochrome powder to produce high nitrogen ferrochrome intermediate material with good quality and controllable material, which is beneficial to the smooth smelting of high nitrogen alloy and high nitrogen steel melt, and can effectively control the chemical composition of high nitrogen steel, and obtain high quality and high quality Nitrogen billet and castings; As the main raw material of high nitrogen steel, micro-carbon ferrochrome powder has wide sources and reliable quality. Compared with the direct use of ferrochrome nitride and high nitrogen ferrochrome raw material, it can reduce the manufacturing cost of high nitrogen billet and castings.
Ferrochrome powder: At present, there are three main smelting methods of low carbon ferrochrome: cold loading method, electric furnace-shaking bag method and oxygen blowing method. Among them, the cold loading method is to add chromium ore, silochrome alloy and lime into the electric furnace to melt the charge, use the silicon in the silochrome alloy to reduce the Cr2O3 in chromium ore, through the desilication and chrome reaction to produce low and medium carbon ferrochrome powder. This method has high power consumption and serious loss. Electric furnace-shaking ladle method is to produce low and medium carbon ferrochrome powder by desilication and chromium-increasing reaction of silicon-chromium alloy smelted from ore furnace through ladle shaking and refining furnace. Compared with cold loading method, energy consumption and ore consumption are greatly reduced. However, the electric furnace-shaking ladle method requires the joint operation of three parts, namely, the silicon-chromium furnace, the refining furnace and the ladle shaking ladle, and there are many production equipment. In the actual production, the linkage of multiple furnaces is required, and the coordination is difficult to grasp. At the same time, the slag abandonment amount is large, and the environment pollution is serious. Oxygen blowing method is also known as "one-step method", is the ore furnace smelting out of high carbon ferrochrome powder directly into the converter for oxygen blowing, the use of oxygen oxidation of carbon, silicon and other elements, do not need silicon chromium alloy intermediate product production link, step to get low chromium iron powder products. The advantages of this method are: the smelting cycle is short, the production rhythm is compact, and the production of the intermediate products without silicon chromium alloy. The energy required by the reaction is the chemical heat generated by itself without additional electric energy. However, the reason why this technology is difficult to be popularized is that when smelting low carbon ferrochrome powder in the traditional converter method in our country, based on the idea that the higher the temperature is more beneficial to decarbonize and restrain the chromium oxidation, the high temperature smelting process is adopted in the actual production process, such as FeCr55C200, the temperature is 1800°C; When FeCr55C100 is produced, the temperature is 1900°C; The temperature is even higher than 2000°C when FeCr55C50 is produced. High blowing temperature not only causes the furnace lining life is short, refractory consumption is large, and the recovery rate of ferrochrome powder is very low, only about 81%.
In the 1970s, Mannion and Fruehan elaborated the principle of using CO2 as the decarbonizing agent of Fe-C melt, and their experimental results showed that about one-fifth of CO2 could be effectively used in the decarbonization reaction. Heise et al. introduced CO2 into AOD refining (argon-oxygen mixed blowing decarbonization) carbon steel, and the results showed that the addition of CO2 improved the decarbonization efficiency of AOD process. The stainless steel melt (Fe-Cr-C chromite powder) was decarbonized by CO2 and O2 mixture gas, and the effect of decarbonization and chromium preservation was obtained. As can be seen from the above, it is feasible to introduce carbon dioxide decarbonization. In addition, through the comparison between pure blowing CO2 and pure blowing O2, it can be seen that by pure blowing CO2, the carbon content decreases from 3% to about 1%, and there is almost no loss of Cr. The loss of Cr in ferrochrome powder is as high as 1.5% when the carbon content of pure blowing O2 decreases from 3% to 1%. Therefore, CO2 has the effect of decarbonization and chromium preservation.
UHT, a Swedish company, has developed a process for smelting low - and medium-chromium iron powder by introducing water vapor into AOD. Since water vapor decomposing at high temperature absorbs heat, the purpose of controlling the molten pool temperature can be achieved by controlling the proportion of water vapor added, which is similar to the introduction of carbon dioxide for smelting.
Prev: Suoyi 100
Next: Silicon Nitride Factory Directly Sale Silicon Nitride Ceramic Material Raw Materials CAS No 12033
Our Contact